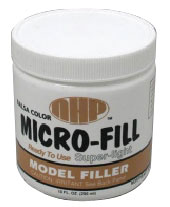
Balsa wood is a very smooth and porous material, curse by some purist (mostly museum quality scale model builder) venerated by other, including myself, It is a very workable product and is very easy to acquire. Unfortunately its grains and pores are always showing after painting, thus divulging the scale of the work. A lot of people had found solutions to hide the grain of the wood, one of them is to apply several layer of CA glue followed with sanding between each layer, I had found this technique to much laborious and smelly. Fortunately for me, I came across this product, Micro-fill for balsa, it is water base and you just have to sand a little after its application, if your patient enough it will hide 100% of the porosity on the wood. For my model discuss here, I applied it only on 55% of the surface, even if this product does miracle for hiding the wood grain I don't particularly love the sanding process, so if you look closely, we can still see some grain on my model.
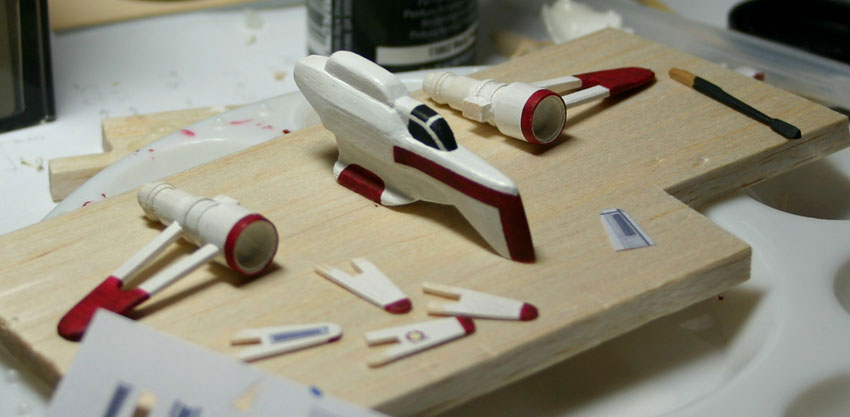
For each glued piece, I had to fill the cracks with the balsa filler, and after sanding everything I applied a full coat of white.
For all the red lines, I've used some 2 mm tape to create really straight patterns (
Fig H). When the 2mm tape was too large I used a special x-Acto to create my own narrow tape stripes (
Fig I).
Fig H
Fig INarrow tape and special X-Acto were bought at
MicromarkThe Balsa filler at a local hobby store.
UdiscoStep 4 to follow (Decals and gluing the ailerons). Back to
Step 2